OUR STORY
Humtown is a family-owned, three generation company that has served the foundry industry for more than 60 years. Watch the video below where Mark Lamoncha, Humtown President & CEO, explains how he and his team turned his father’s humble pattern shop into a global leader in conventional and 3D printed sand cores & molds.
1959
Humtown’s family-owned, three generation legacy stems back to 1959, when Russell Lamoncha opened a small pattern shop in Columbiana, OH. Then called Humtown Pattern, Russell and a partner operated out of a small garage on the same property where they are located to this day. Russell’s son Mark Lamoncha was able to grow up working in and learning the family business from a young age.
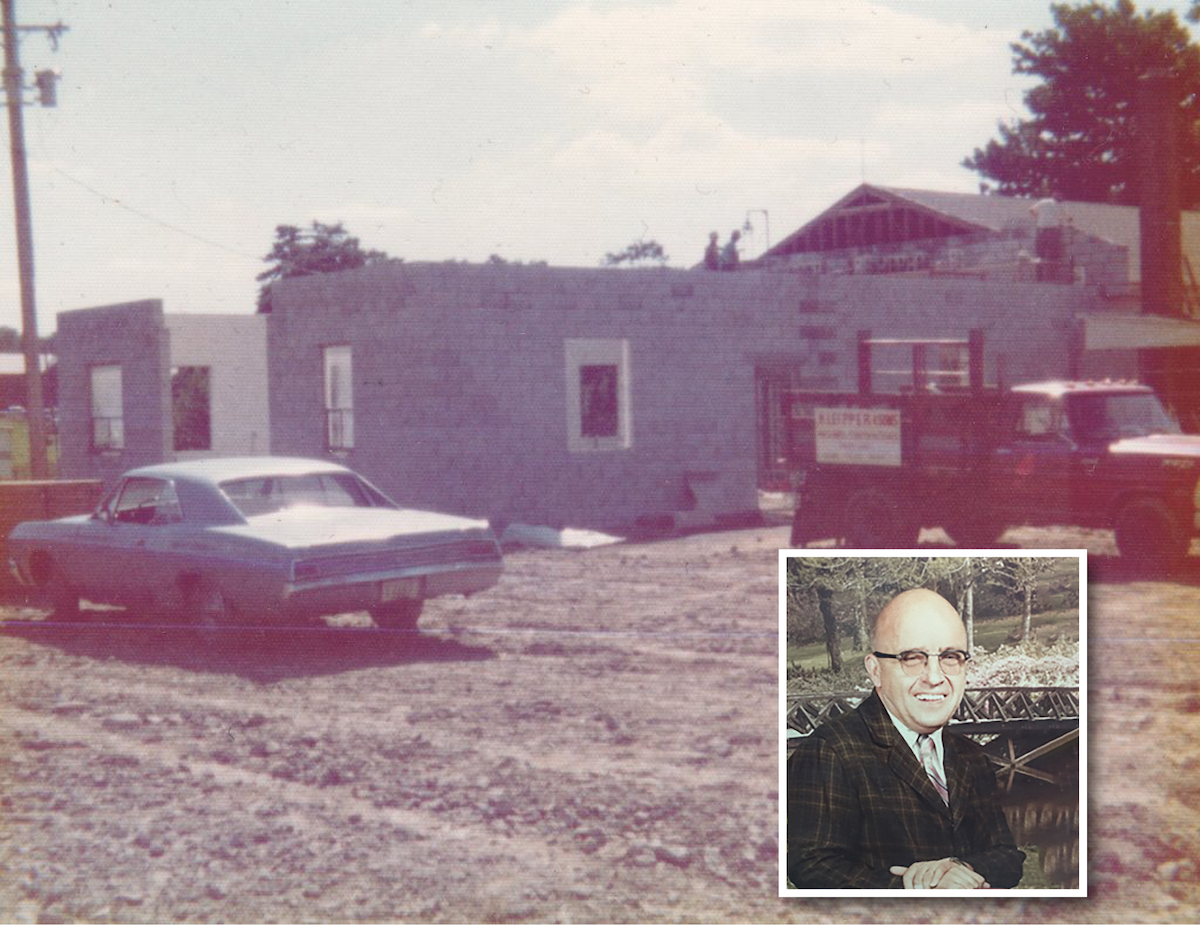
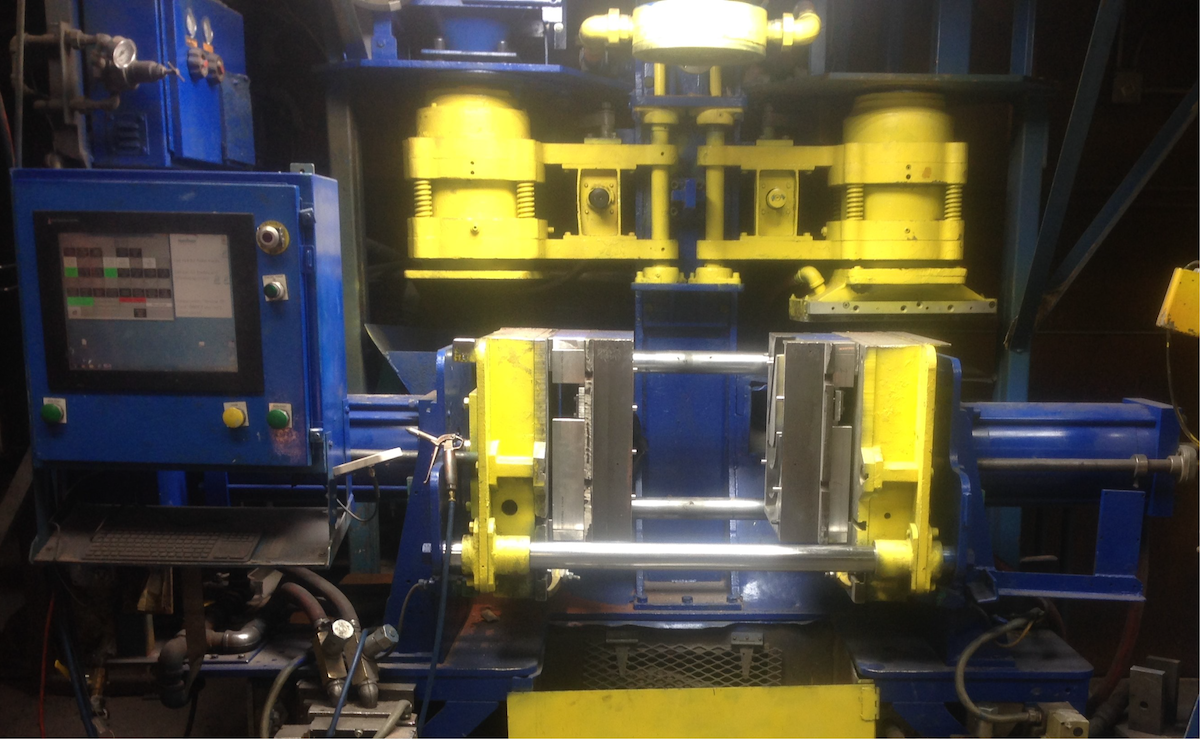
1977
In 1977, Mark wanted to expand the company beyond traditional pattern making. Mark was more interested in technology, innovation and machinery, and was drawn to a new but related industry – sand core and mold production, with a new name called Humtown Products. Still working with foundries, they used a traditional blowing process to create air-set and cold-box sand cores and molds.
2008
Not long after the financial markets crash of 2008, Mark was desperate to prevent Humtown from going into bankruptcy. After much prayer, Mark created the framework of what would become the Visual Earnings System, a now patented method of dramatically improving productivity by enhancing Humtown’s workforce through technological innovation. This real-time process of measuring and showing team member’s their rate of productivity would result in sustained increases in productivity of 250 to 400 percent.
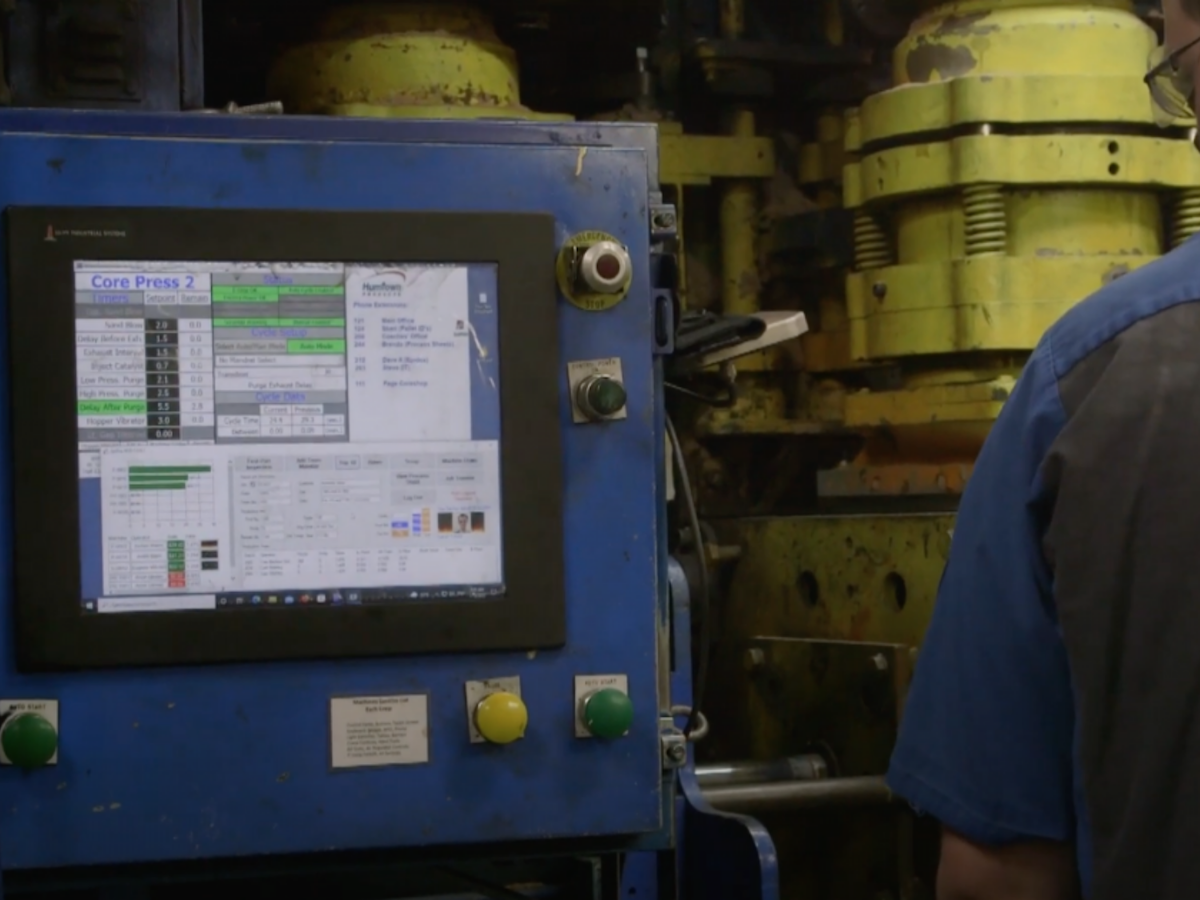
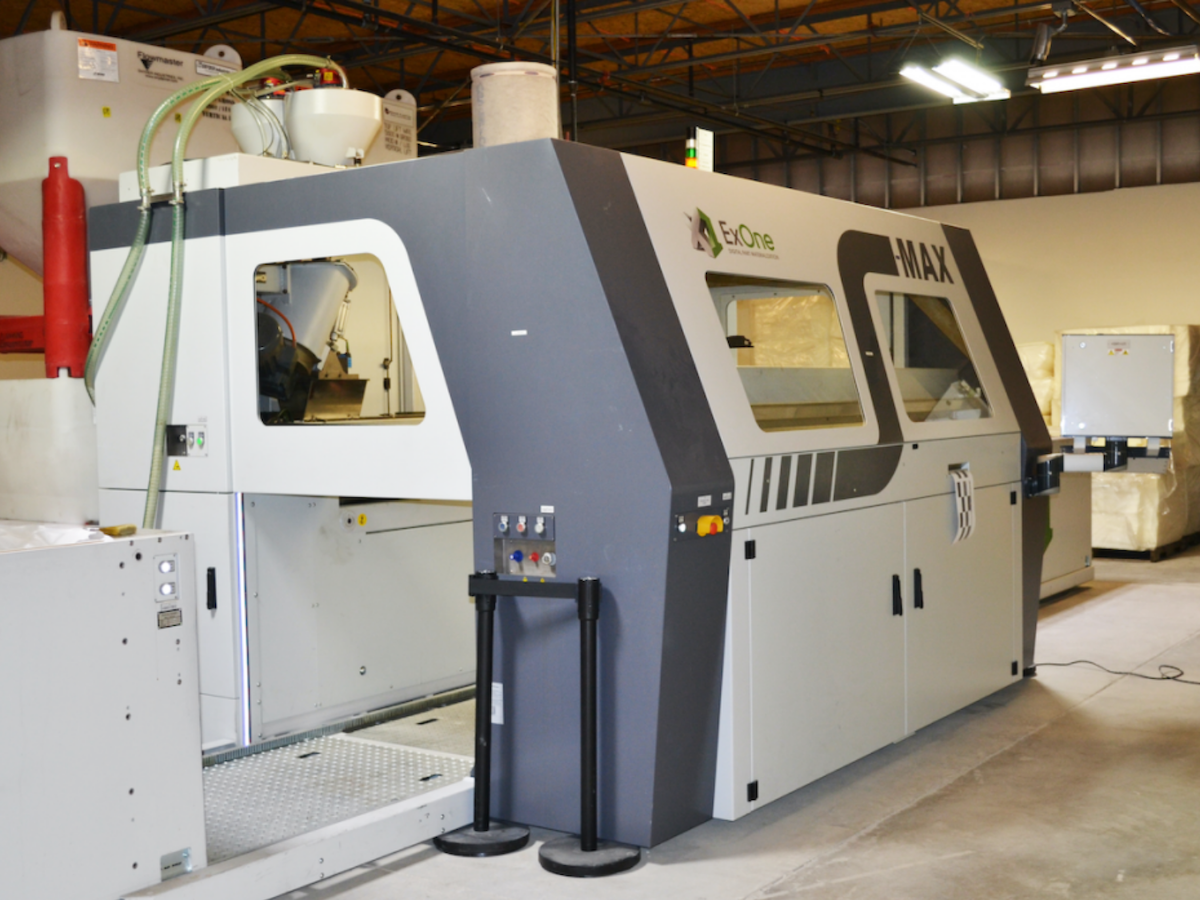
2014
In steps Humtown Additive, a division of Humtown that specializes in the additive manufacturing of sand cores and molds. Humtown received their first sand 3D printer back in 2014 through a partnership with Youngstown State University. Since then Humtown Additive has continued to add to its fleet, now housing the most 3D sand printers under one roof in North America, maybe the world.
2018
As demand for Humtown Additive’s 3D printed sand cores and molds started to explode, they quickly outgrew their manufacturing facility. In 2018, they moved out of their old facility and into a massive 100,000 sq ft facility located in Leetonia, OH. This gave them room to expand both to their 3D printer fleet and their production capacity.
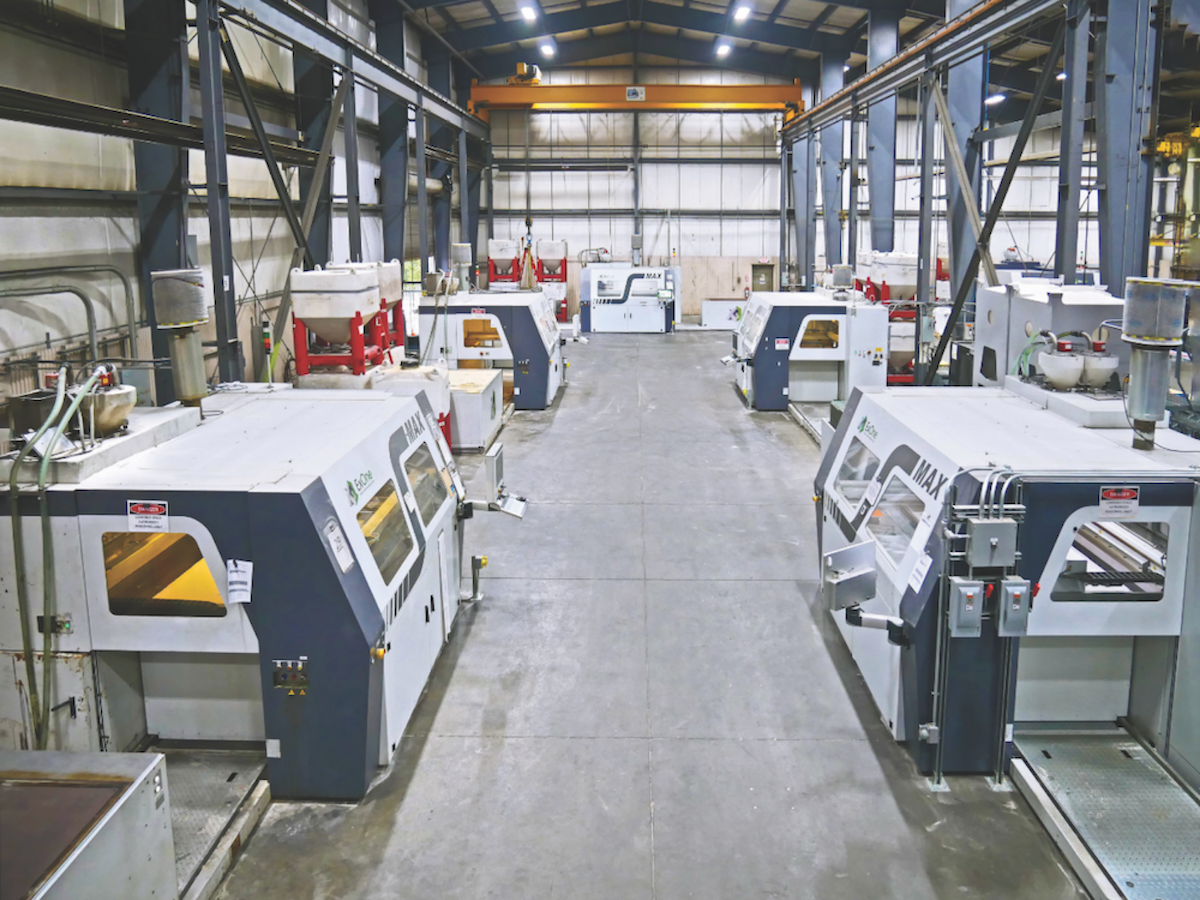
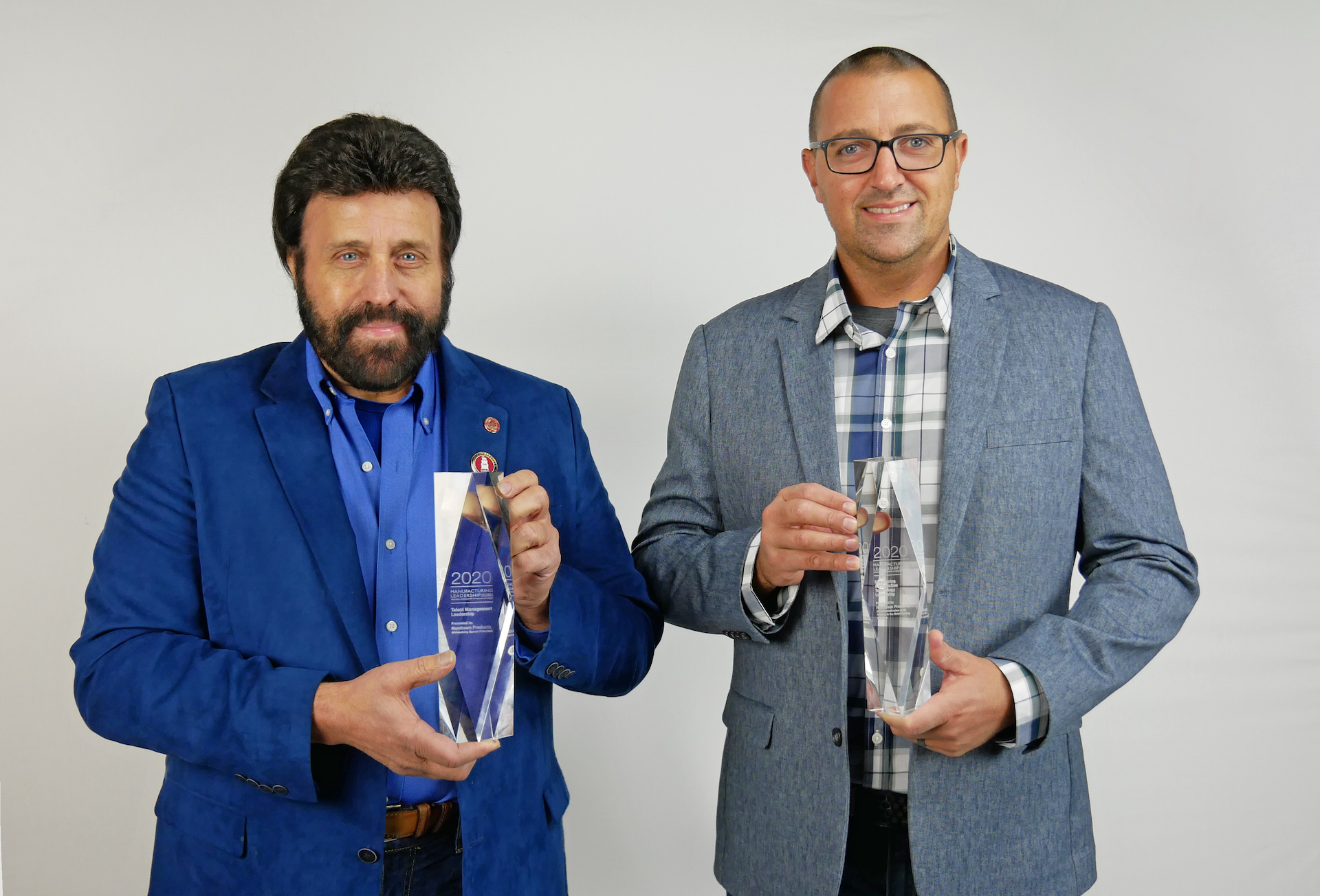
2020
After almost a decade of relentless technological innovation, Humtown Additive’s success culminated in 2020 when they won the National Association of Manufacturers (NAM) 2020 Manufacturer of the Year in the small to medium enterprise category. In making this selection, NAM’s panel of expert judges specifically cited Humtown’s utilization and commercialization of 3D sand printing.
2024
Ever growing and always pushing the boundaries of technology, Humtown Additive’s increasing demand for 3D sand printing necessitated a move to a much larger facility in 2024. Not only is there space to accommodate Humtown Additive’s continued growth, but the new location boasts a full atmospheric control system that will guarantee more optimized sand printer efficiency. This move to Boardman Ohio, into a former chocolate factory, is the key to continue Humtown Additive’s sweet success for years to come.
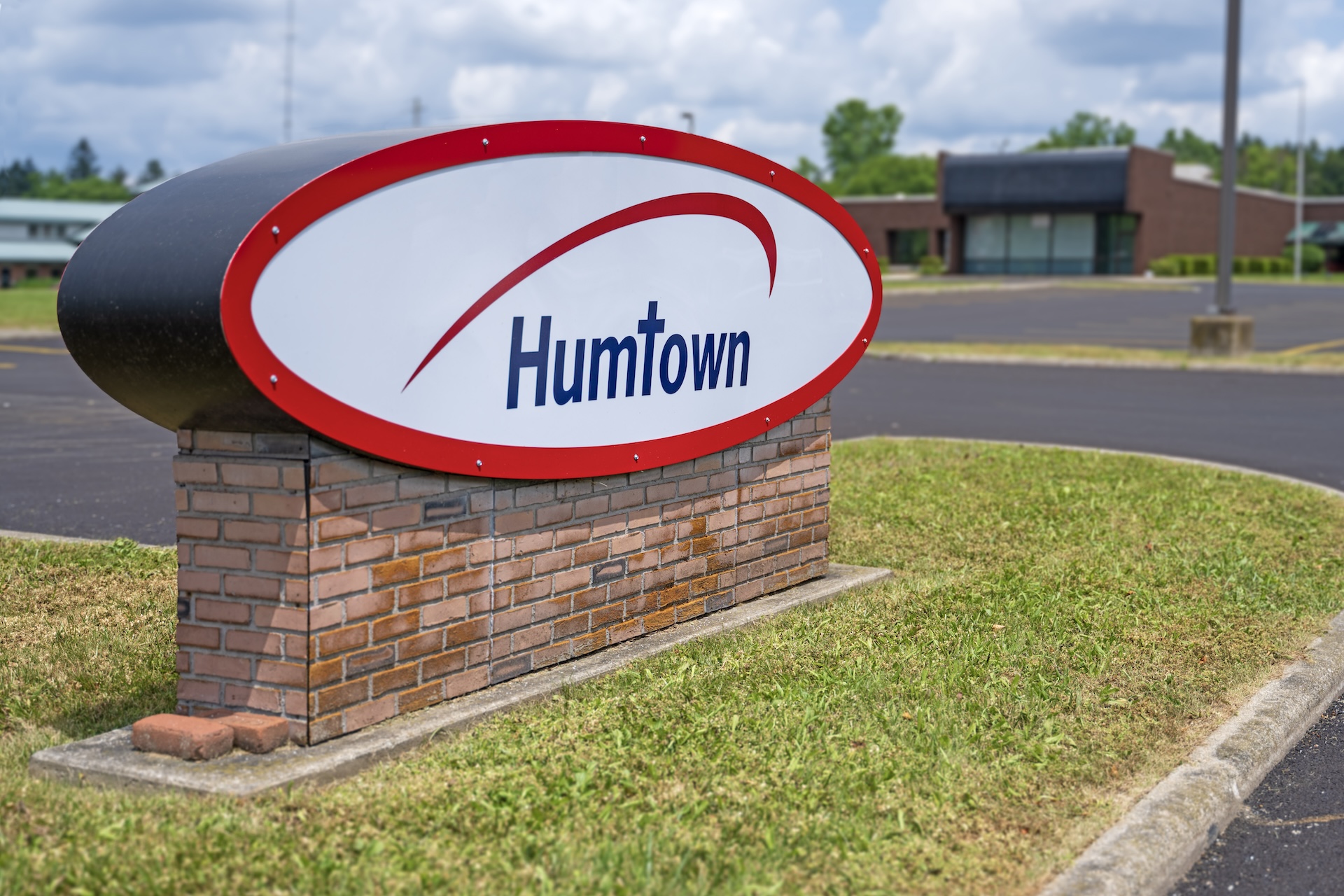
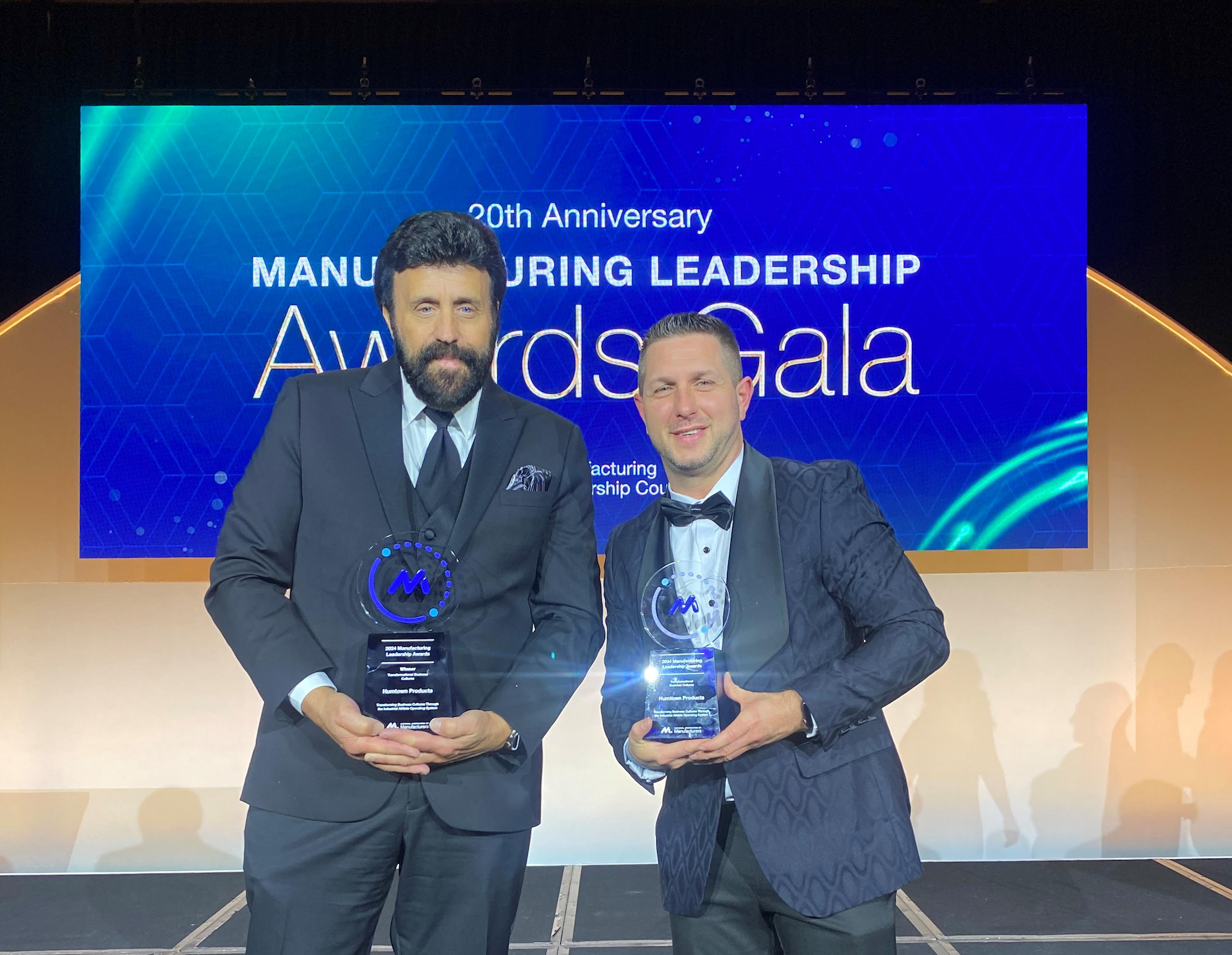
2024
In 2024, the National Association of Manufactures (NAM) honored Humtown once again — awarding Mark Lamoncha, President and CEO, the Transformational Business Cultures award for creating the Industrial Athlete Operating System™. Mark was honored to receive this award along with Tim Figley, co-author of the book they wrote to document this holistic, transformative process — The Industrial Athlete Operating System: Where Human Performance Empowers Industry 4.0. Mark was humbled by the experience and stated, “It’s an honor to accept this award on behalf of our amazing team. This recognition underscores our relentless pursuit of unlocking our team members God-given potential, which is the cornerstone of Humtown’s culture. We believe in ValYouShip, valuing each person above all else, because innovation and technology will never surpass the value of a human being.”
1959
Humtown’s family-owned, three generation legacy stems back to 1959, when Russell Lamoncha opened a small pattern shop in Columbiana, OH. Then called Humtown Pattern, Russell and a partner operated out of a small garage on the same property where they are located to this day. Russell’s son Mark Lamoncha was able to grow up working in and learning the family business from a young age.
1977
In 1977, Mark wanted to expand the company beyond traditional pattern making. Mark was more interested in technology, innovation and machinery, and was drawn to a new but related industry – sand core and mold production, with a new name called Humtown Products. Still working with foundries, they used a traditional blowing process to create air-set and cold-box sand cores and molds.
2008
Not long after the financial markets crash of 2008, Mark was desperate to prevent Humtown from going into bankruptcy. After much prayer, Mark created the framework of what would become the Visual Earnings System, a now patented method of dramatically improving productivity by enhancing Humtown’s workforce through technological innovation. This real-time process of measuring and showing team member’s their rate of productivity would result in sustained increases in productivity of 250 to 400 percent.
2014
In steps Humtown Additive, a division of Humtown that specializes in the additive manufacturing of sand cores and molds. Humtown received their first sand 3D printer back in 2014 through a partnership with Youngstown State University. Since then Humtown Additive has continued to add to its fleet, now housing the most 3D sand printers under one roof in North America, maybe the world.
2018
As demand for Humtown Additive’s 3D printed sand cores and molds started to explode, they quickly outgrew their manufacturing facility. In 2018, they moved out of their old facility and into a massive 100,000 sq ft facility located in Leetonia, OH. This gave them room to expand both to their 3D printer fleet and their production capacity.
2020
After almost a decade of relentless technological innovation, Humtown Additive’s success culminated in 2020 when they won the National Association of Manufacturers (NAM) 2020 Manufacturer of the Year in the small to medium enterprise category. In making this selection, NAM’s panel of expert judges specifically cited Humtown’s utilization and commercialization of 3D sand printing.
2024
Move to new 3D printing facility in Boardman, Ohio.
2024
National Association of Manufacturers (NAM) award in the category of Transformational Business Cultures for the proprietary Industrial Athlete Operating System™.
3D Printed Sand
Cores & Molds
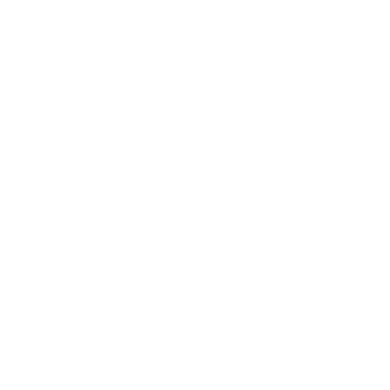
We have commercialized 3D sand printing, producing strong and complex cores and molds without tooling.
Conventional Sand
Cores & Molds
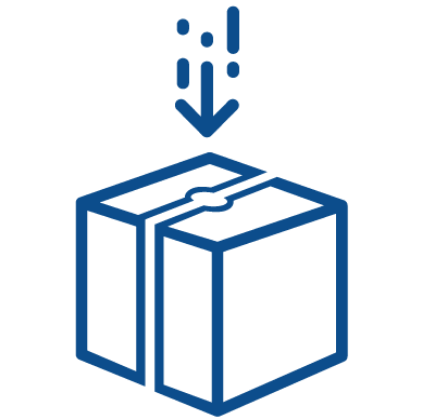
Serving the foundry industry for over 60 years, we specialize in conventional cold box and air-set cores & molds.
unitube blow
tube system
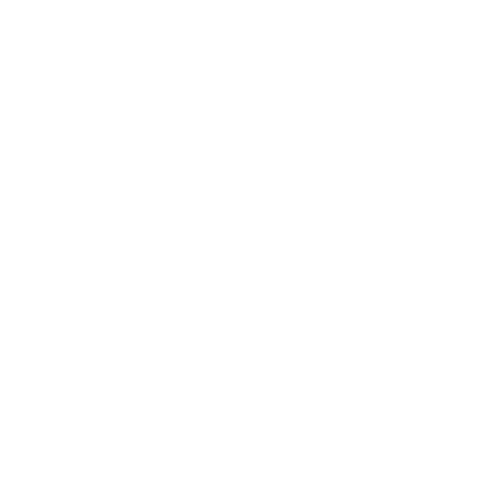
Our UNItubes replace metal blow tubes, simplifying foundries’ production processes & increasing profits.